- Home
- Know-how
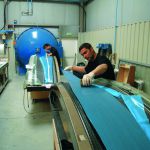
Pre-impregnated
We produce a large number of components in carbon fibre (and glass fibre) fabrics using a method that involves the laying-up of pre-impregnated composites. The pre-impregnated fabrics are made using fibres of composite materials impregnated with resin during the course of manufacture which means that no further resin needs to be added when the components are manufactured
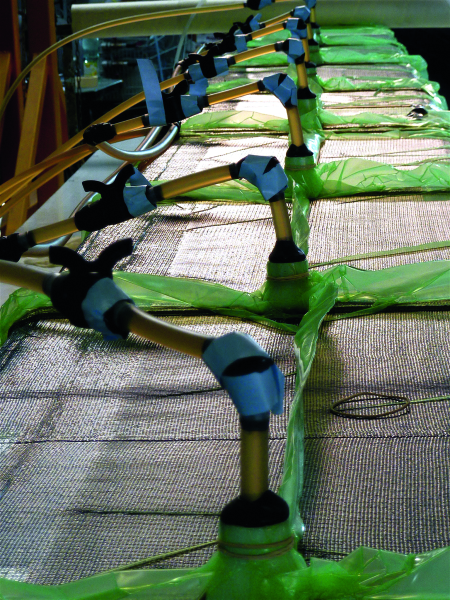
Infusion, RTM, and RTM Light composites
The infusion technique enables fabrics made of composite materials to be vacuum moulded. By using this technique, the components are left with a very homogeneous distribution of resin with an extremely low porosity rate. All of the tools used for autoclave production processes are made using the infusion technique.
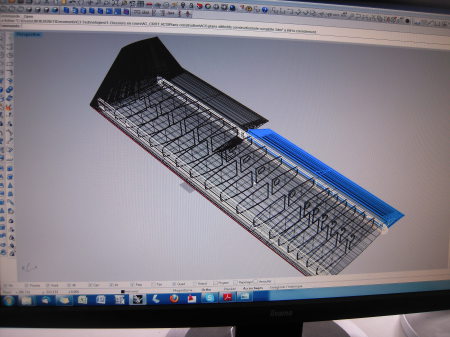
Computer assisted design and manufacture
Working from the drawings supplied, the team at C³ Technologies uses computers to design, programme and machine the pre-forms and moulds needed to produce the required components. We break the component down into manufacturing steps, starting with the architects’ (or designers’) drawings before working out, designing and conducting the machining and digital cutting operations. Our software enables us to utilise and create 2D and 3D models.
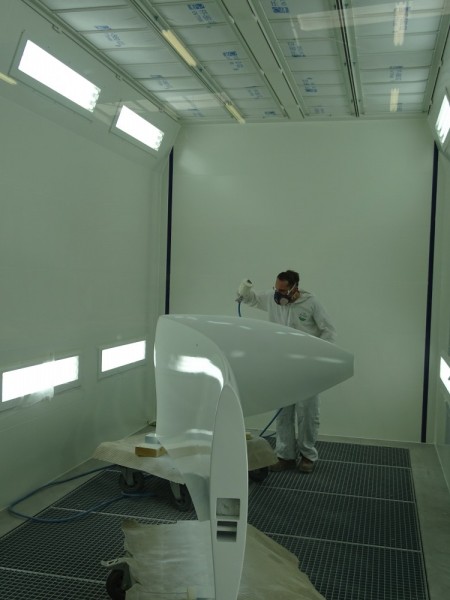
Coatings preparation and finishing of parts
Surface preparation enables parts to be made watertight or to help products that are to be applied at a later stage to achieve a better hold. To better meet the client’s requirements, a spray gun is used so that parts can be coated with the product best suited to their requirements, leaving them with a perfect and aesthetically attractive surface finish.
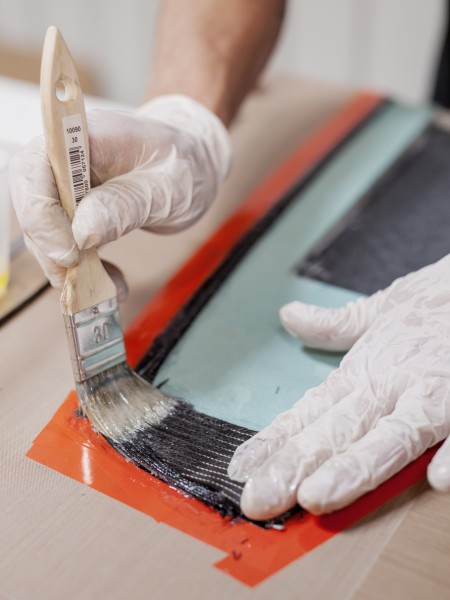
Vacuum moulding
Wet moulding is the manual application of resin (by means of brushes or rollers) to different types of fibre reinforcements. The fibres are then compacted when a vacuum is created and the surplus resin released is impregnated into a special absorbent felt.